Lykkegaard has just had a new Okuma CNC lathe with milling function installed at the factory.
Among other things, it will be used to turn items such as pump housings, axle equipment and pump hubs, which will be used for the propeller pumps that are produced at the factory in Ferritslev.
Some of the advantages are, that it can make work more efficient, increase accuracy and improve the working environment.
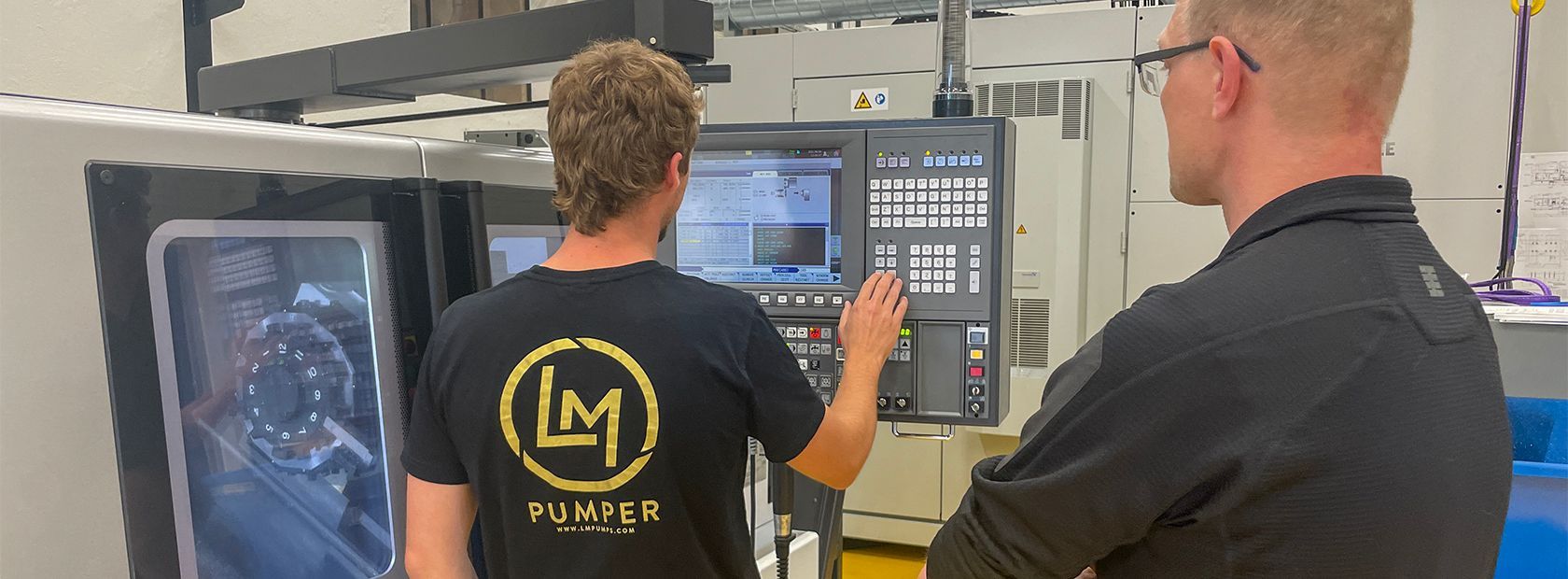
Behind the closed doors, the workpieces move around, while the machine's tools work quietly and precisely. With the help of computer programming, the machine knows exactly how to process the workpiece, which tools to use and very precisely what dimensions the workpiece should have when it is finished.
Industrial technician Nicolai Burmeister sets up the programs and keeps an eye on the machine.
The new machine, Okuma LB3000, can effectively turn pump blanks – and is particularly effective when several similar blanks are to be processed. And then it improves the working environment.
Until now, employees have had to turn, drill and ream manually, which cannot avoid releasing metal dust particles into the air. Particles which are now kept inside the machine and which will therefore not disturb the employees' airways or require different cleaning than that which is in the machine.
Investment and labor shortage
The machine can also improve efficiency and lower production costs in a time of labor shortages.
“It will do some work that would otherwise have been done by apprentices or journeymen in the factory. It would have been bad style to replace people with machines if we had had a surplus of labour. But in a time when it is difficult to fill industrial technician positions, and there are not enough applicants for the training, it is also a way to make the factory work with the hands we have," says director Karsten Lykkegaard.
Lykkegaard Pumper exclusively produces customized propeller pumps and therefore does not have mass production of exactly the same items. Therefore, they have been a little unsure whether a CNC lathe was an obvious choice. Eight years ago, they bought an older and used model to test it on work methods and workflows. It has worked fine - but partly the programming is out of date, and partly it was located far from the company's large five-axis CNC milling machine, so when Nicolai Burmeister has to teach apprentices how to program, they are physically far apart. In addition, the new machine can be more precise and accurate in its processing than the old one.
The new machine is therefore located right next to the CNC milling machine, so that apprentice and journeyman are close to each other, and so that one person can often operate both machines.
STAY UP TO DATE!
Sign up for our newsletter to receive our inspirational stories. You will hear from us a couple of times a year.